The return of Urban Manufacturing
Through the spread of new technology and readily available information about how to use it, new small and medium-scale manufacturing companies are not only starting to appear in our cities, but are attracting a new generation of young entrepreneurs to the industry.
With global interconnectedness and technological advances - particularly those in digital fabrication - manufacturing has changed massively from its 20th century counterpart (1). It requires less staff, space and initial investment, and is much easier to manage.
Firstly, manufacturing capabilities have increased dramatically. What was once done with tens of machines and people can now be done with two or three machines and minimum staff to look after them. The cost of these machines has also been rapidly decreasing (2). Furthermore, looking after every stage of production has also become simpler with affordable and easy to use cloud-based software, which makes ordering, stocking & production and finance-management cheaper and simpler (2). All of this means that the whole process can be directed by smaller teams: “Three guys with laptops used to describe a Web start-up. Now it describes a hardware company, too”
Factories are also requiring less space - with on-demand manufacturing reducing the need for both material and stock storage. Whole products can also be made at a single location - think micro-factories making everything from knitwear to microchips and cars.
But what has really given confidence and inspiration to future manufacturers is all the information made freely available through an ‘Open Making’ movement - concerned with the use of these new technologies. A whole range of companies are not only showcasing their products, but their entire supply chain including processes and equipment involved (e.g. Ajoto, Peachy Printer & many Kickstarter projects). Complex production processes have been demystified.
There is a growing wealth of information ranging from how to use software, choose and set up various machines (CNC routers, laser cutters, electric weavers, etc.) and fit-out premises. Production-ready and tested designs for complex products which can be easily manufactured with the most commonly used fabrication tools are accessible for free through platforms like Opendesk, Wikihouse or OS Vehicle, to name just a few. These designs can be studied, improved and even altered by users, potentially making something completely different out of them. In addition, the Open Making community provides informal support to new and existing “members” through both online, regular events and new physical infrastructure like shared workshops and maker-spaces. An older generation of manufacturers is also becoming more open and visible through platforms such as Fabhub, 100k garages, and Make Works.
It is important to emphasize the role of the customer, whose interest in production has also been growing, partly as a reaction to very complicated - and at times opaque and questionable - practices being followed by Big Business. More people want to know how their products were made, and the demand for locally made goods is on the rise in the UK and US.
These are the changes that are making it easier to set-up a manufacturing business and for young people to enter the sector, not only as apprentices, but also as entrepreneurs. New manufacturing companies don’t have to be on the outskirts, or have large, new or expensive premises. They can be located around city centers, close to both users and other industries and networks. We are already seeing examples of such companies in UK cities with their goods selling both nationally and internationally. Pimoroni is making a variety of microchips and electronics in a small warehouse next to Sheffield City Centre, with more than 20 people and a compact army of high-tech machines - thanks to a number of successful Kickstarter campaigns.. Even in the very centre of London, Unmade is making customizable CNC-knitted clothing right in the middle of Somerset House. Could manufacturing become the next regeneration driver for western cities?
Our experience with ChopShop can also be presented as an example here. Consisting of a starter-level CNC router and a few hand tools, ChopShop was set up in 2012 to provide an affordable design and digital fabrication service to creatives and start-ups. Production levels have been growing and this summer we have cut our second Wikihouse. But it is the time-frame of the project that is interesting: fabrication of all the parts for a house made of 500 plywood sheets was possible on a single machine costing less that £10,000 in a space of 6 weeks – all in a small warehouse next to Sheffield City Centre.
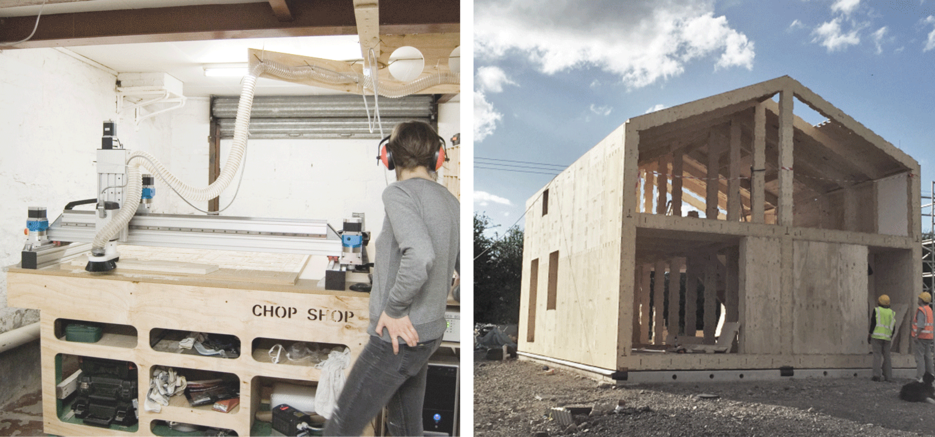
This is not to say that manufacturing has become simple however – just that different skills are now required. Design is key and nothing can be done without the knowledge of various CAD, design and software packages, marketing and communication. Not to mention great work flexibility (no regular 9 to 5) and a “can-do” attitude!
The next few year will be very exciting with governments and businesses across the US and Europe investing a lot of money into a “hardware renaissance” (3). It would be interesting to see if new manufacturing clusters will emerge, or to see how small workshops can work together to produce larger complicated products or really huge orders. Can all the parts for an airliner be made locally and then only assembled in a hanger next to an actual run-way? We are at the point when there is now huge potential to alter and grow local production and manufacturing, supporting local economies in creating exciting jobs for a younger generation.
References:
(1) SIE (2015): Making good our future
(2) Sabhlok, Raj (2014): The Frugal Cloud: Powerful Business Software On The Cheap, Forbes.
(3) Foroohar, Rana & Saporito, Bill (2013): Made in the U.S.A. Time.