Meet the Makers: Scott at Housefish
We caught up with Scott from Housefish to talk about ethical supply chains, life in Denver and the cross-over between Formula One cars and furniture!
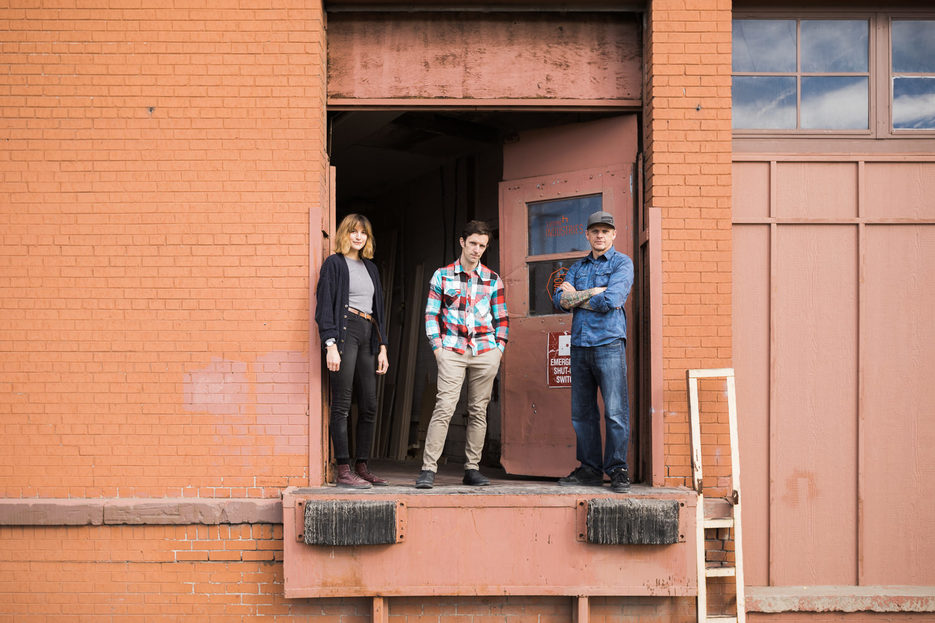
Opendesk: When did you make your first foray into the world of making?
Scott: Growing up I loved Formula One racing. I’d often wake up at 6am in the morning just to catch a race. I went on to study auto engineering at Loughborough University, which took me into the world of racing in 1996. Unfortunately, it was the worst moment to be entering the field right after the famous “split” where Indianapolis Motor Speedway broke away from the CART IndyCar Series. I was on the breakaway side, working for a company called G Force. I then went over to the US to work on Indy Cars, and even worked on a few aeroplanes over there, but it became obvious that racing wasn’t going to be as much fun as I thought. They were changing all the rules, slowing all the cars down and essentially changing the bits about the sport I loved most. Through some connections I ended up doing some freelance furniture design engineering.
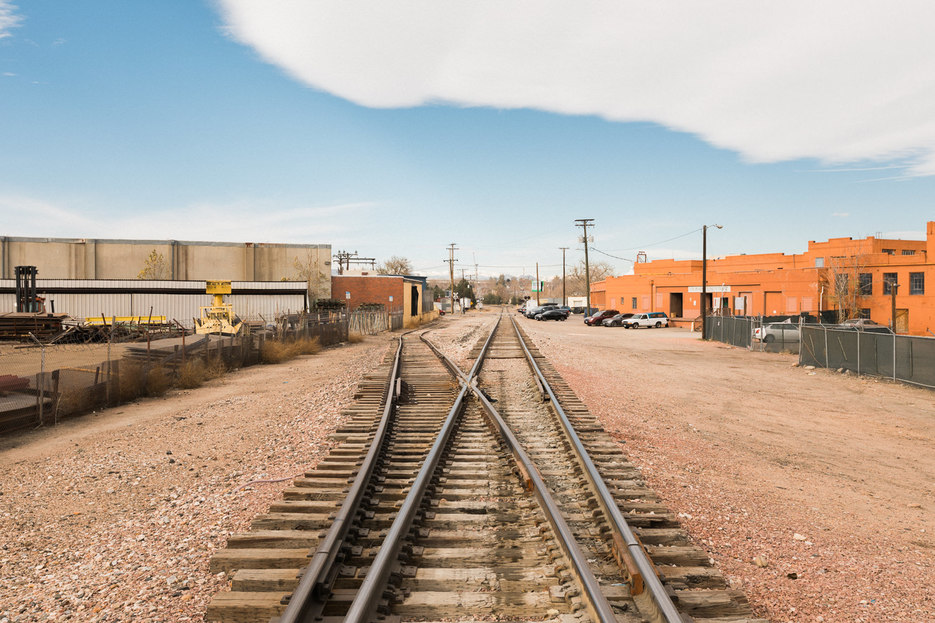
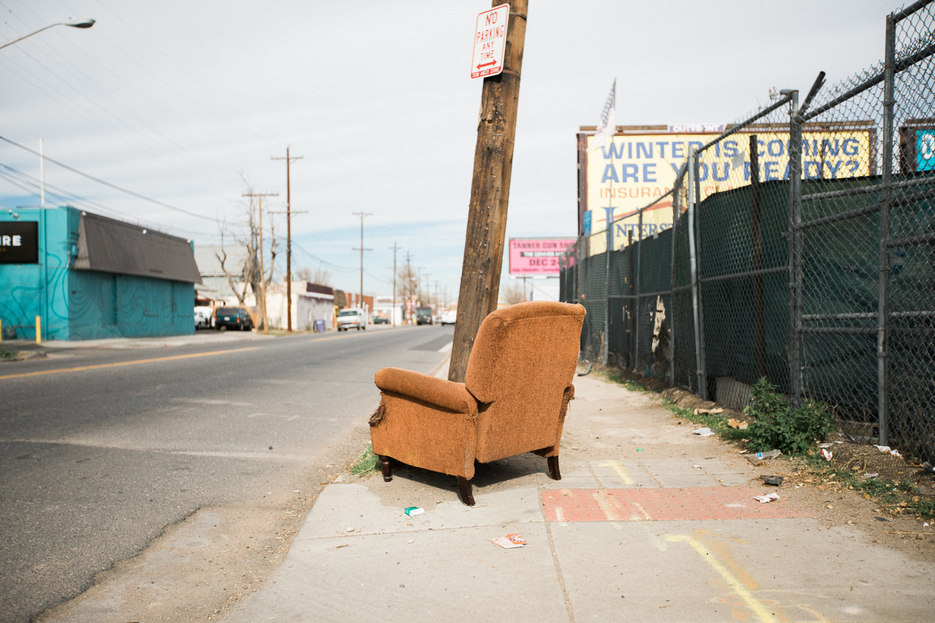
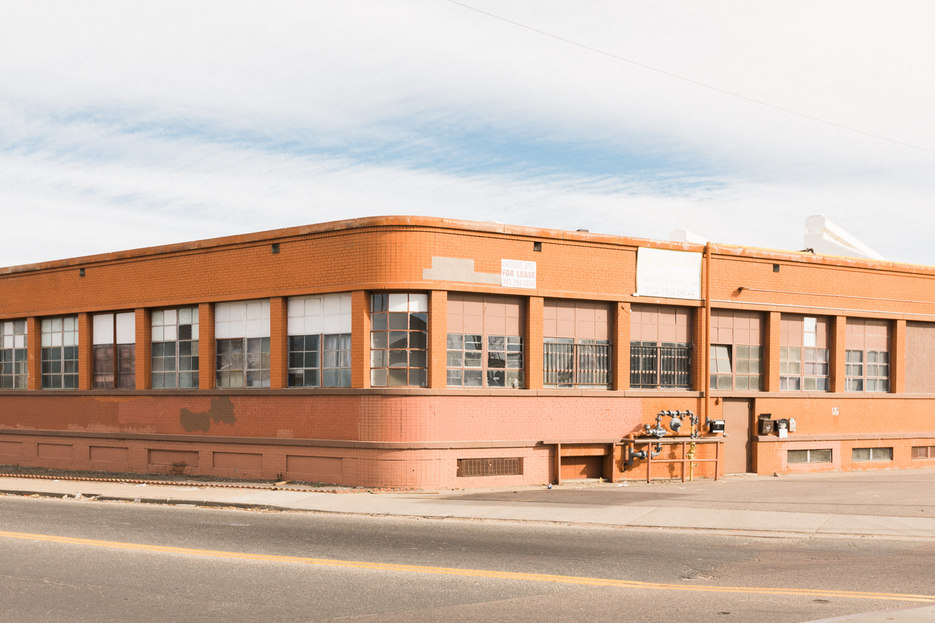
Opendesk: Is that when you decided to start Housefish?
Scott: I actually co-founded a baby furniture company in 2005 next and we manufactured everything in Vietnam, where I’d visit a few times a year. We were operating in a much better way than the other factories you’d find there, but I still found it a little disheartening and it became apparent quickly that the supply chain could be better.
Opendesk: What about the process was disheartening?
Firstly, there were the environmental impacts from moving goods around the globe multiple times to save money. Trees would be cut down in North America, shipped to Asia where labour costs are cheaper, turned into furniture then shipped back. Conditions in factories also aren’t great and the nature of the work is very repetitive, which bothered me on a human level. It drove us to ask why buy anything from an automated factory overseas? Why not do it locally?
I started to think about how we could move things back to the US and do it better. Obviously the days of Henry Ford style factories weren’t an option, but I knew CNC from my racing days so we decided to combine the two! All materials were FSC certified and flat packed. It really was groundbreaking 10 years ago, people just weren’t doing it and thinking of digital fabrication that way yet.
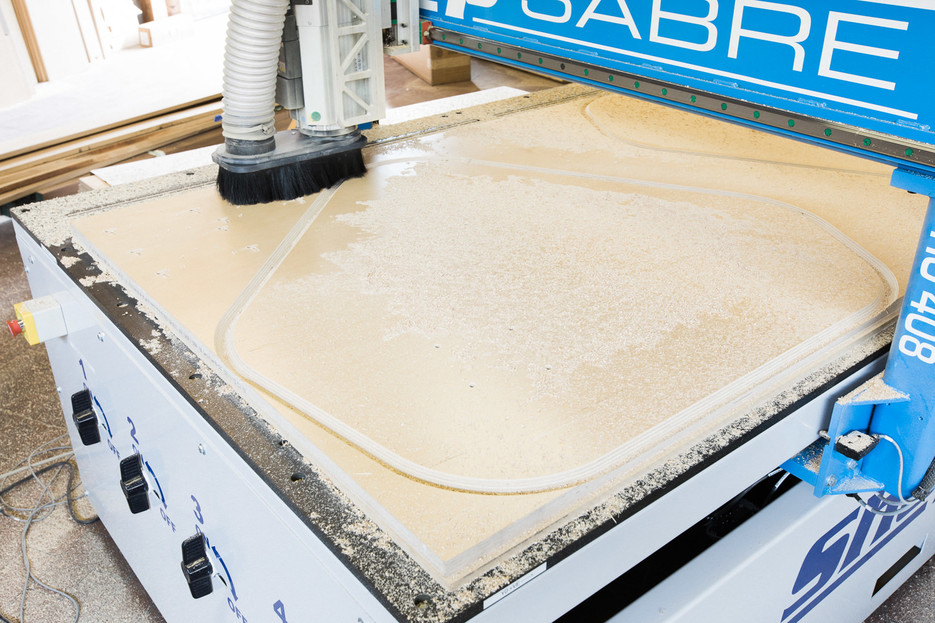
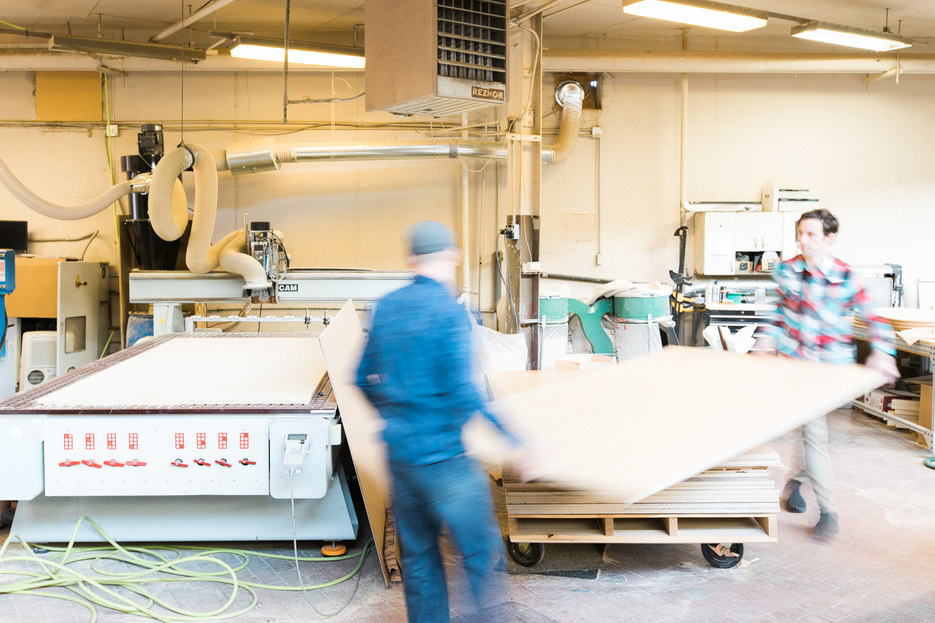
It was just me starting out. I designed a product that was viable and had a local company CNC the parts. I ordered a few sheets of materials, put it on a credit card and stored everything in my garage, from where it was built and shipped.
We did that enough times to be able to buy our own CNC machine, and it’s really just been upwards since then. We specialise in furniture but also do a bit of architectural fabrication, which I just view as furniture attached to a building anyway.
“It drove us to ask: why buy anything from an automated factory overseas? Why not do it locally?’
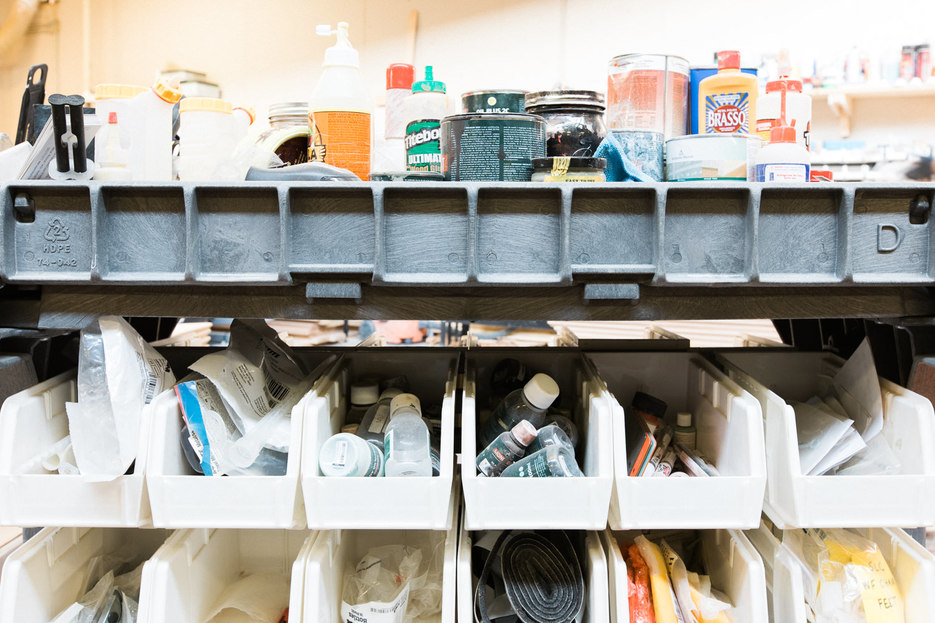
Opendesk: Tell us about the work Housefish did for one of our clients, Wunder Werkz, making Cafe Tables and Linnea Bookshelves?
Scott: Sure. TAXI is a large community space that was formerly a yellow cab HQ in Denver. It’s been restored and is now a thriving retail, residential and business hub. We supplied all the furniture for the suites in the latest building to launch: Flight. That’s the biggest Opendesk project we’ve had to date and it was great to work on something at a much larger scale.
The client loved it too as it was truly local. When they had questions, they could just come over to have a look at things – whether that’s finishes or design features. We could walk to the project from our shop and it was great for us to be so close to the source of production. At the end, we just drove it round and set it up!
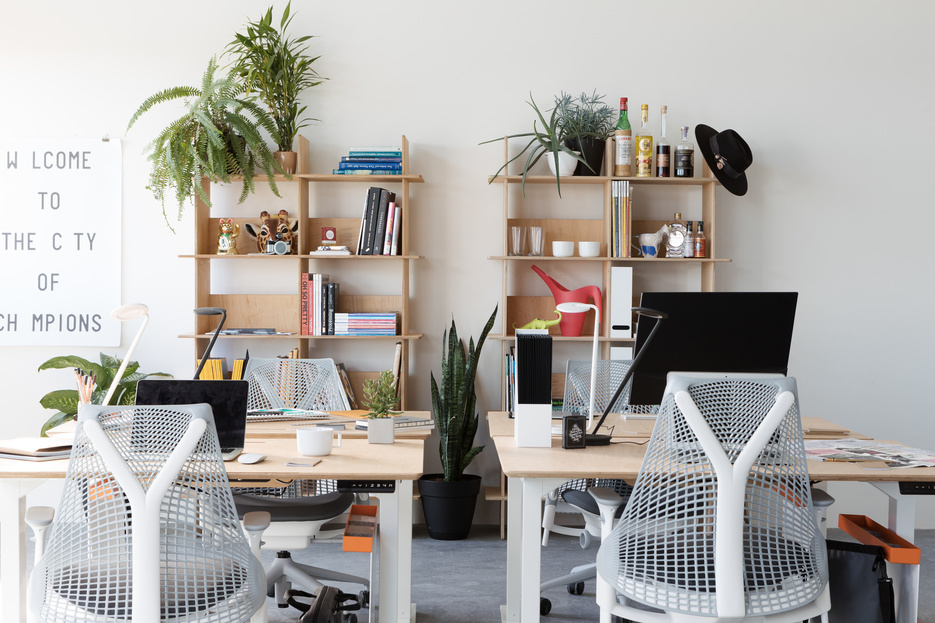
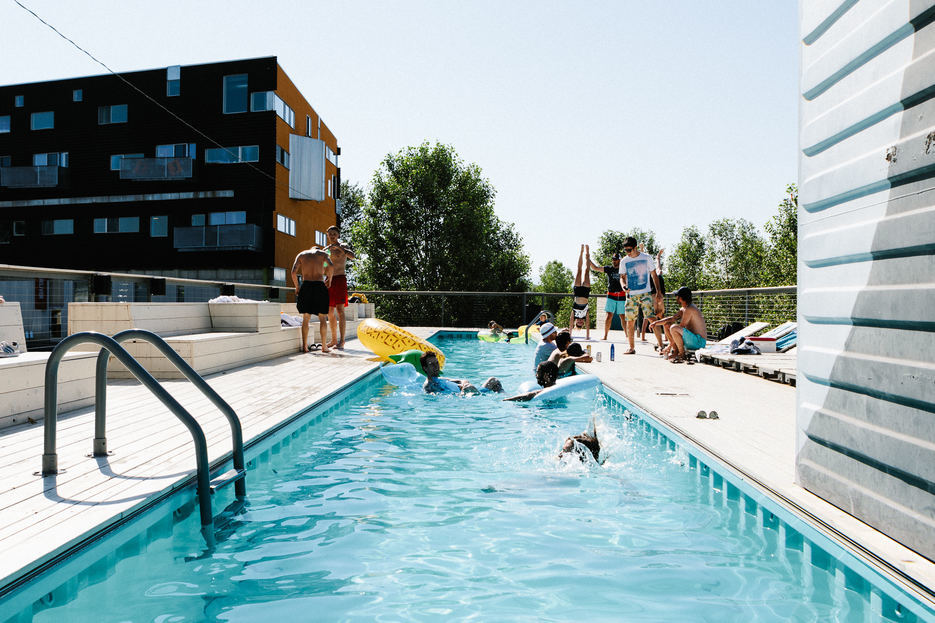
Opendesk: What drove you to join Opendesk as a maker?
Scott: I signed up as a maker on Opendesk three years ago. It initially sparked my interest because it seemed like a good fit. I like the concept of distributed manufacturing in general and it’s cool to see it evolve and become interesting in different ways, so I thought I’d give it a try! There are commercial aspects too obviously, and with the Wunder Werkz project Opendesk has become a big part of our business.
“We could walk to the project from our shop and it was great for us to be so close to the source of production.”
Opendesk: Tell us a bit about what is Denver like. Is the making movement taking off there?
Denver has a really interesting history with downturns punctuated by explosive growth. It was founded as a mining camp during the gold rush, which came and went and died. Then there was the silver rush 20 years later and another subsequent boom then downturn, then the oil boom, which followed a similar path. Telecommunications bolstered the economy for a while and there was a mini marijuana rush (we were one of the first stated to legalise it). With the growth you get great and interesting energy, but it also squeezes a lot of people out which is a shame.
When I was growing up here it was pretty backwards. It certainly wasn’t cool and people mostly wanted to get out – myself included. But it feels like it’s grown into itself and is certainly one of the hottest cities in the US at the moment. It’s attractive to designers, to people want to make things and to people building companies. It’s a great place for us to be doing what we’re doing.
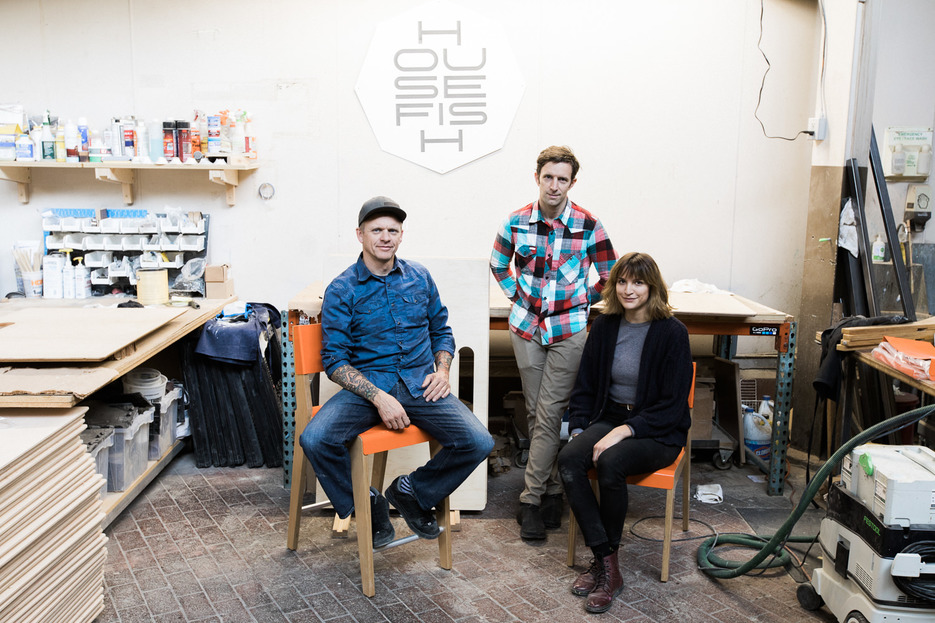
Designs featured in this article:
Photography by JC Buck